Subtle Glimpses of the Project.
Advantis Quartz, the Flagship brand in India is the leading manufacturer of raw materials for quarries and its engineering, whilst exporting its high-end products to various countries across the world. Struggling with disjointed workflows, lesser employee efficiency, and errors in the process, they reached out to Sanskar technolab for the development of a universal platform to manage end-to-end business operations.
Client Location
Udaipur, Rajasthan.
Tech-Stack
Web Server: Frappe Cloud
Database: MySQL (Maria DB)
ERPNext Version: 14.13.0Industry
Manufacturing & Export
Project Methodology
Agile Scrum Methodology
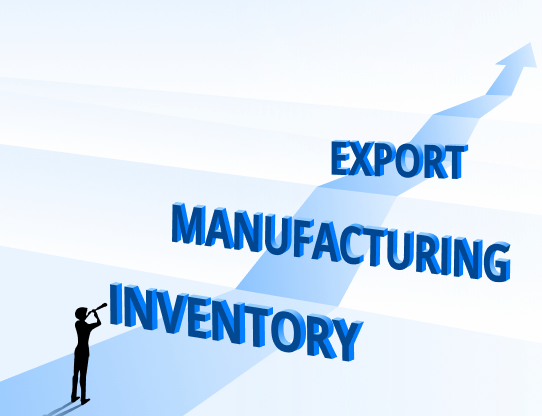
Clients Vision & Mission!
Advantis Quartz (Advance Surfaces) is a high-end flagship brand owned by two significant Natural Stones enterprises, The Mumal Marble Group and The Arihant Group, two of the world’s most well-known natural stone businesses.
Lokesh Modi, the accounts head at Advantis Quartz reached out to Sanskar technolab with their challenges when it comes to managing manufacturing, inventory, exports, etc, looking for a solution to have one universal platform in place to simplify their business processes and optimize operations.
Our Work!
Lokesh Modi, the Accounts Department Head reached out to the team at Sanskar Technolab through their website. We have connected with their team management, and employees and even visited the site to understand their business requirements to offer solutions accordingly.
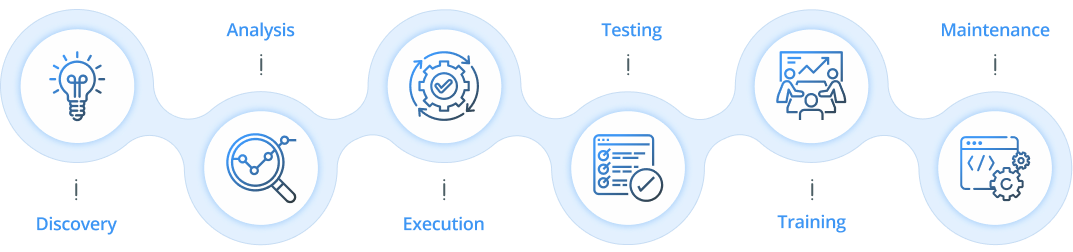
Using the Numbers Magic: Here’s what our client has achieved!

21%
Increase in employee efficiency with one universal solution to manage business workflows.

15%
Over 15% cost savings with better process and module management.

78%
Increase in employee retention due to automated processes.

54%
Boost in Customer Satisfaction due to better quality assurance and structured processes.
Some of the out-of-the-box features we have implemented for our client!

Automating the bonuses
Increase in employee efficiency with one universal solution to manage business workflows.

Gratuity calculations made easy
ERPNext ensures automated and accurate gratuity calculations.

Conversations at the core
Precise unit conversion management and smooth transitions between units, leading to better inventory management and sales accuracy.

Automated Re-ordering
Optimized inventory levels with automated re-order functionalities.

Serial-number-wise tracks
Serial-number-wise inventory management for precise control and enhanced visibility over every single item in the inventory.

Supplier Grading Scorecard
Developed customized supplier scorecard for grading based on key parameters such as material quality, delivery time, user ratings, and payment terms considered for comprehensive supplier assessment.
The Range of Modules we have implemented for our client!
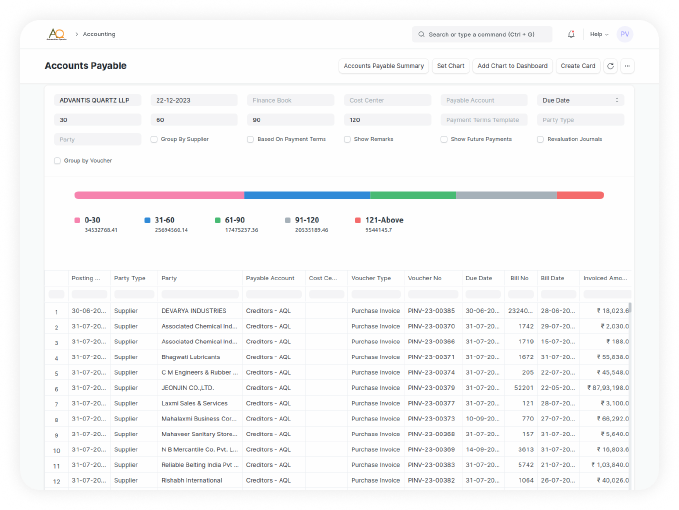
In the Account Module, Advancis Quartz relies on ERPNext for effective payment and bill tracking, management of payables and receivables, and monitoring overdue times. ERPNext's robust features contribute to streamlined financial processes, enhancing overall business operations.
- Payment and bill tracking
- Management of payables and receivables
- Monitoring of overdue times
- Multi-currency billing system for seamless management with export countries.
Before vs After: Courtesy Sanskar Technolab’s ERPNext Implementation!

Procurement and inventory management were heavily reliant on manual processes, leading to inefficiencies and time delays.

Procurement & Inventory
After ERPNext implementation, procurement processes and real-time inventory tracking are automated, leading to reduced manual efforts and time consumption.
Lack of real-time data visibility poses a problem for decision-making, making it challenging to respond swiftly to market demands.

Visibility of Operations
ERPNext provided comprehensive real-time data visibility through intuitive dashboards and graphical representation, empowering quick and informed decision-making for improved agility.
Supplier performance evaluation lacked a structured approach, resulting in inconsistent material quality and delivery delays.

Better supplier management
The introduction of ERPNext's supplier scorecard enhanced the assessment of material quality, delivery times, and payment terms, ensuring a consistent and reliable supply chain.
Financial tracking relied on multiple systems, leading to complexity and difficulty in monitoring payables and receivables.

Finance Management
Centralized financial tracking in ERPNext streamlined the monitoring of payables and receivables that too in different currencies as per requirement, simplifying overall financial management.
Before
Procurement and inventory management were heavily reliant on manual processes, leading to inefficiencies and time delays.
After
After ERPNext implementation, procurement processes and real-time inventory tracking are automated, leading to reduced manual efforts and time consumption.
Before
Supplier performance evaluation lacked a structured approach, resulting in inconsistent material quality and delivery delays.
After
The introduction of ERPNext's supplier scorecard enhanced the assessment of material quality, delivery times, and payment terms, ensuring a consistent and reliable supply chain.
Before
Financial tracking relied on multiple systems, leading to complexity and difficulty in monitoring payables and receivables.
After
Centralized financial tracking in ERPNext streamlined the monitoring of payables and receivables that too in different currencies as per requirement, simplifying overall financial management.
What Our Client Loved Throughout the Project?

Customizations
Our client has chosen us as their ERPNext implementation partner due to our commitment to providing tailored solutions. Understanding that every business has unique requirements, we specialize in customizations that align seamlessly with the specific needs of their business.

The transition from Excel and Other Systems
Advantis Quartz was seeking a comprehensive solution to replace their existing dependence on Excel and another purchase management system. Sanskar technolab presented ERPNext as the universal answer to their diverse needs. Our expertise in managing transitions from legacy systems to unified convinced our client to choose us as their ERPNext implementation partner.

Site Visits
Sanskar Technolab went the extra mile by conducting on-site visits to our client's businesses, gaining an in-depth understanding of their unique operations and project requirements. Seeing things in action helps us understand what they need. This personalized approach was a key factor in their decision-making process.
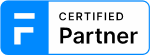
ERPNext Bronze Partner
The fact that Sanskar Technolab is a leading ERPNext Partner was a key deciding factor for our client. This official partnership not only signifies our recognized expertise in ERP implementation but also adds a layer of trust and assurance to the entire process. Being an official partner assured our client that they are collaborating with a team of professionals with the backing and support of the ERPNext platform.
The challenges of Advantis Quartz and Solutions of Sanskar Technolabs!
Challenge | Solution | |
---|---|---|
![]() Unoptimized Production Planning |
The client faced inefficiencies in production planning, leading to resource wastage and operational bottlenecks. | Sanskar technolab initiated a detailed assessment of the client's production processes. Understanding the intricacies, our team customized the ERPNext module to provide a tailored solution for better planning and resource tracking. The result was a streamlined production process with optimized resource utilization, improving overall efficiency. |
![]() Problems with Managing Cash Flow |
The client lacked a robust cash flow reporting system for effective financial management. | Recognizing the need for detailed financial insights, Sanskar technolab collaborated closely with the client's finance team. We implemented a highly functional cash flow reporting system within ERPNext, providing the client with comprehensive financial data for better management decisions and a clearer financial overview. |
![]() Limited Resource Tracking |
The client faced challenges in efficiently tracking and managing the inventory, order, sales, and purchase. | Sanskar technolab worked closely with the client's operations and resource management teams. Customized resource tracking features were implemented within ERPNext with material weightage, gate in and out for both purchase and sales along with end-to-end Quality assurance for optimal resource utilization and improved overall management. |
![]() Quality Grading Disparities |
Varying quality grading for manufactured products makes the process of managing inventory inefficient and full of errors. | Sanskar technolab customized the module for managing different grading products in a structured and seamless manner. This ensured standardized quality across different manufacturing specifications, enhancing customer satisfaction and brand reputation. |
![]() Unit Measurement Complexities |
Challenges arose due to different units of measurement in the purchase and selling processes. | Sanskar technolab addressed this challenge by implementing a unified unit conversion feature in ERPNext. This streamlined the purchase and selling processes, ensuring consistency and accuracy in unit measurements, and simplifying overall inventory and sales management. |
![]() Managing quotations & currencies of different countries |
Managing orders, invoices, and quotations across different countries and currencies posed a significant challenge for the client, introducing complexities and potential errors. | With ERPNext’s features and our team expertise, we have implemented a simple yet effective process for managing orders, invoices, and quotations from different countries and currencies effectively. The result is a system that facilitates smooth and error-free transactions, enhancing overall operational efficiency for the client. |

Unoptimized Production Planning
Challenge
The client faced inefficiencies in production planning, leading to resource wastage and operational bottleneck
Solution
Sanskar technolab initiated a detailed assessment of the client's production processes. Understanding the intricacies, our team customized the ERPNext module to provide a tailored solution for better planning and resource tracking. The result was a streamlined production process with optimized resource utilization, improving overall efficiency.

Problems with Managing Cash Flow
Challenge
The client lacked a robust cash flow reporting system for effective financial management.
Solution
Recognizing the need for detailed financial insights, Sanskar technolab collaborated closely with the client's finance team. We implemented a highly functional cash flow reporting system within ERPNext, providing the client with comprehensive financial data for better management decisions and a clearer financial overview.

Limited Resource Tracking
Challenge
The client faced challenges in efficiently tracking and managing the inventory, order, sales, and purchase.
Solution
Sanskar technolab worked closely with the client's operations and resource management teams. Customized resource tracking features were implemented within ERPNext with material weightage, gate in and out for both purchase and sales along with end-to-end Quality assurance for optimal resource utilization and improved overall management.

Quality Grading Disparities
Challenge
Varying quality grading for manufactured products makes the process of managing inventory inefficient and full of errors.
Solution
Sanskar technolab customized the module for managing different grading products in a structured and seamless manner. This ensured standardized quality across different manufacturing specifications, enhancing customer satisfaction and brand reputation.

Missing CRM and POS
Challenge
The absence of Customer Relationship Management (CRM) and Point of Sale (POS) systems hindered customer management and payments. This gap in technology impacted the overall customer experience and the efficiency of payment processes.
Solution
ERPNext introduced CRM and POS modules, addressing the lack of customer management and payment efficiency. It leads to a better overall customer experience, allowing for better communication and streamlined payment processes.

Managing quotations & currencies of different countries
Challenge
Managing orders, invoices, and quotations across different countries and currencies posed a significant challenge for the client, introducing complexities and potential errors.
Solution
With ERPNext’s features and our team expertise, we have implemented a simple yet effective process for managing orders, invoices, and quotations from different countries and currencies effectively. The result is a system that facilitates smooth and error-free transactions, enhancing overall operational efficiency for the client.